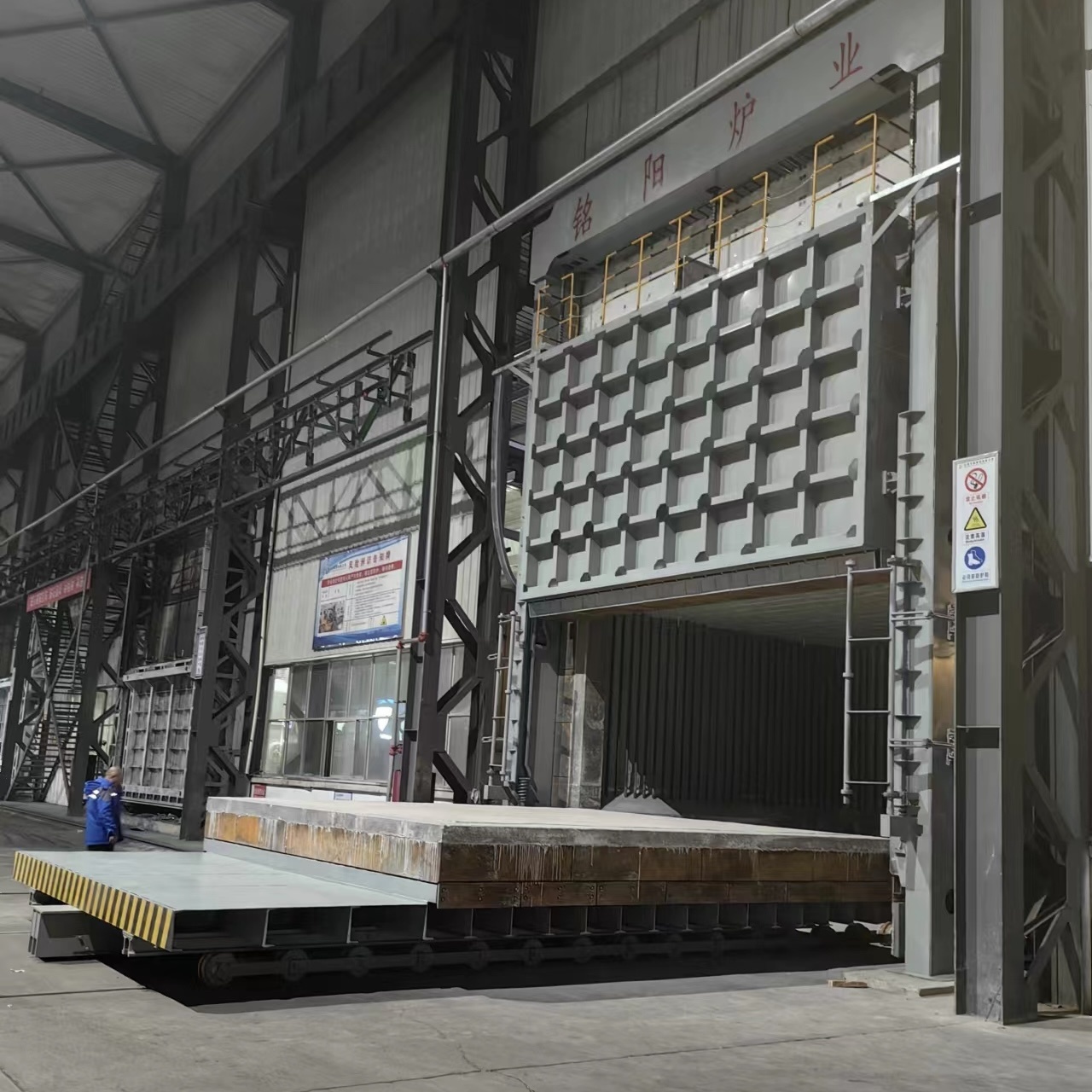


Unlocking Efficiency: The Benefits of Using a Wholesale Nitriding Furnace
Unlocking Efficiency: The Benefits of Using a Wholesale Nitriding Furnace
Table of Contents
1. Introduction to Nitriding Furnaces
2. What is Nitriding?
3. Key Benefits of Using Nitriding Furnaces
4. Why Opt for Wholesale Nitriding Furnaces?
5. Cost-effectiveness and Return on Investment
6. Applications of Nitriding Furnaces in Various Industries
7. Choosing the Right N
Unlocking Efficiency: The Benefits of Using a Wholesale Nitriding Furnace
Table of Contents
- 1. Introduction to Nitriding Furnaces
- 2. What is Nitriding?
- 3. Key Benefits of Using Nitriding Furnaces
- 4. Why Opt for Wholesale Nitriding Furnaces?
- 5. Cost-effectiveness and Return on Investment
- 6. Applications of Nitriding Furnaces in Various Industries
- 7. Choosing the Right Nitriding Furnace for Your Needs
- 8. Maintenance Tips for Nitriding Furnaces
- 9. Frequently Asked Questions
- 10. Conclusion
1. Introduction to Nitriding Furnaces
In today’s competitive industrial landscape, maximizing efficiency while maintaining product quality is essential. **Nitriding furnaces** stand out as a pivotal technology in the heat treatment sector, particularly for enhancing the hardness and fatigue resistance of metal components. This article explores the myriad benefits of utilizing a wholesale nitriding furnace, shedding light on how this technology can propel your manufacturing processes to greater heights.
2. What is Nitriding?
Nitriding is a specialized **heat treatment process** that enhances the surface hardness of metals through the diffusion of nitrogen into the material. This process typically occurs at lower temperatures compared to other heat treatment methods, making it energy-efficient. The result is a hard, wear-resistant surface that significantly extends the lifespan of components, making nitriding particularly valuable in applications where durability is paramount.
The Nitriding Process Explained
The nitriding process involves several key stages:
1. **Preparation**: Components are thoroughly cleaned to remove any contaminants.
2. **Heating**: Items are heated in a controlled atmosphere, usually at temperatures ranging from 500 to 600 degrees Celsius.
3. **Nitrogen Diffusion**: Nitrogen is introduced into the furnace environment, allowing it to permeate the surface of the metal.
4. **Cooling**: Parts are slowly cooled to room temperature, solidifying the hardened layer.
This method is particularly beneficial for materials such as alloy steels, tool steels, and certain types of cast iron.
3. Key Benefits of Using Nitriding Furnaces
The use of nitriding furnaces offers numerous advantages that can significantly impact your production line:
Enhanced Hardness and Wear Resistance
One of the most notable benefits of nitriding is the creation of a hardened surface that resists wear and tear, which is crucial for components subjected to friction and stress. This enhancement allows for longer service life and reduced replacement costs.
Improved Fatigue Strength
Nitriding enhances the fatigue strength of parts, reducing the likelihood of failure under cyclic loading conditions. This is particularly important in applications involving gears, crankshafts, and other components that experience repeated stress.
Lower Processing Temperatures
Unlike traditional heat treatment processes that require high temperatures, nitriding occurs at lower temperatures, leading to reduced energy consumption and shorter cycle times. This efficiency translates into cost savings and increased productivity.
Minimal Distortion
The nitriding process minimizes changes to the dimensions of the parts, ensuring that they maintain their original specifications. This aspect of nitriding is vital for industries where precision is crucial.
Environmentally Friendly
Nitriding furnaces are often designed to minimize environmental impact. They use less energy compared to other heating processes and can incorporate systems to reduce emissions, aligning with modern sustainability practices.
4. Why Opt for Wholesale Nitriding Furnaces?
Choosing a **wholesale nitriding furnace** offers several strategic advantages:
Cost Efficiency
Purchasing a nitriding furnace in bulk can lead to significant cost savings. Wholesale options often provide better pricing structures, allowing businesses to invest in high-quality equipment without exceeding their budgets.
Access to Advanced Technology
Wholesale suppliers typically offer the latest models equipped with cutting-edge technology. This access ensures that manufacturers can leverage the best features available, enhancing their production capabilities.
Support and Maintenance
Reputable wholesale suppliers often provide robust customer support, including installation and maintenance services. This support is crucial for ensuring that the furnace operates optimally throughout its lifespan.
5. Cost-effectiveness and Return on Investment
Investing in a nitriding furnace is not just an operational decision; it’s a financial one. Here’s how it can provide a strong return on investment (ROI):
Reduced Operational Costs
The efficiency of nitriding furnaces means lower energy bills and reduced wear on equipment. This efficiency lowers the total cost of ownership, making nitriding a financially sound choice.
Increased Production Efficiency
With faster processing times and enhanced product quality, companies using nitriding furnaces can increase their throughput. Higher production rates lead to greater sales potential and profitability.
Longer Product Lifespan
The durability provided by nitriding processes results in fewer failures and replacements. This longevity translates into significant savings over time, as businesses spend less on maintenance and new parts.
6. Applications of Nitriding Furnaces in Various Industries
Nitriding furnaces are incredibly versatile and find applications in numerous sectors:
Aerospace Industry
In the aerospace sector, components must withstand extreme conditions. Nitriding enhances the durability of parts such as gears, landing gear, and structural components.
Automotive Industry
The automotive industry relies on nitriding for critical parts like camshafts, crankshafts, and transmission components to ensure they can handle high-performance demands without failure.
Manufacturing and Tooling
Many manufacturing applications utilize nitriding to harden cutting tools, dies, and molds, extending their life and maintaining precision during operation.
Medical Equipment
In medical device manufacturing, nitriding can improve the performance and longevity of surgical instruments and implants, ensuring safety and reliability.
7. Choosing the Right Nitriding Furnace for Your Needs
Selecting the appropriate nitriding furnace involves considering several factors:
Capacity Requirements
Assess the volume of production and the size of components to determine the furnace capacity necessary to meet your operational needs.
Type of Nitriding Process
Different nitriding processes (gas nitriding, plasma nitriding, etc.) have unique benefits. Choose a furnace that aligns with your specific process requirements.
Automation and Control Features
Modern nitriding furnaces come equipped with advanced automation features for process control. Evaluate these options to improve efficiency and consistency.
8. Maintenance Tips for Nitriding Furnaces
Regular maintenance is essential for ensuring the longevity and optimal performance of nitriding furnaces:
Routine Inspections
Conduct periodic inspections to identify any potential issues before they escalate. This practice helps maintain consistent performance.
Cleaning and Calibration
Keep furnaces clean and properly calibrated. Regular cleaning prevents contamination, while calibration ensures precise temperature and atmosphere control.
9. Frequently Asked Questions
What materials are suitable for nitriding?
Nitriding is typically effective on alloy steels, tool steels, and certain cast irons.
How does nitriding compare to other heat treatment methods?
Nitriding offers lower processing temperatures and minimal distortion compared to methods like quenching and tempering.
What is the typical cycle time for nitriding?
Cycle times can vary but typically range from a few hours to several days, depending on the material and thickness.
Is nitriding environmentally friendly?
Yes, nitriding processes can be environmentally friendly due to lower energy usage and reduced emissions.
What are the signs that a nitriding furnace needs maintenance?
Signs include inconsistent performance, unusual noises, and temperature fluctuations.
10. Conclusion
Investing in a **wholesale nitriding furnace** is a strategic decision that can yield significant benefits across various industries. From enhanced component durability and cost savings to increased production efficiency, the advantages of nitriding are manifold. As manufacturers continue to seek ways to improve their processes and products, the role of nitriding furnaces will undoubtedly remain paramount. By selecting the right equipment tailored to your operational needs and maintaining it properly, you can unlock a new level of efficiency in your manufacturing processes.