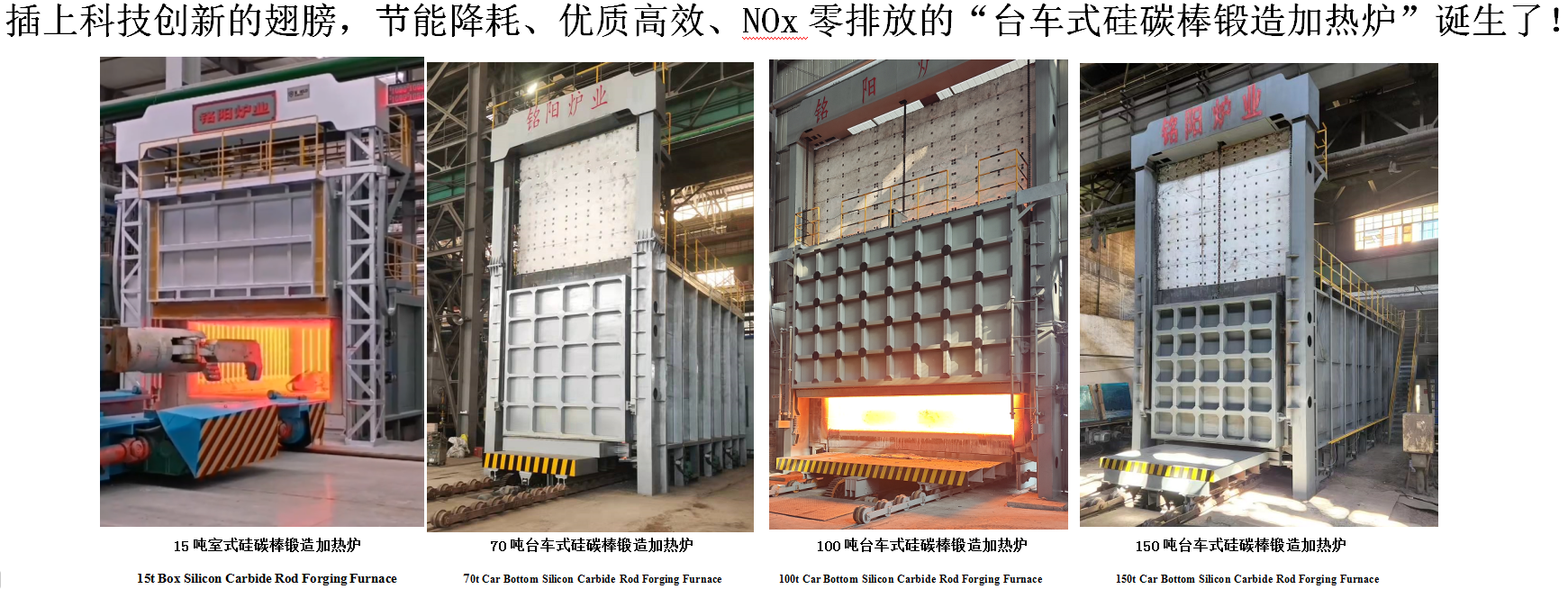


The Latest Innovations in Ladle Preheaters: Enhancing Efficiency in Foundry Operations
Ladle preheaters are essential components in modern foundry operations, playing a critical role in the preparation of molten metal for casting. The newest ladle preheaters utilize advanced technologies to enhance the efficiency and effectiveness of the metal pouring process. By preheating the ladles, these systems significantly reduce thermal shock and improve the overall quality of the cast products.
One of the primary functions of a ladle preheater is to maintain the temperature of molten metal during transfer from the furnace to the pouring location. When metal is poured into a cold ladle, it can cause rapid cooling, leading to unwanted solidification or defects in the casting. The latest ladle preheating technologies address this challenge by utilizing high-efficiency heating methods, such as infrared heating and convection systems, which provide uniform heating across the ladle surface.
These innovative ladle preheaters are designed with energy efficiency in mind. By optimizing the heating process, they minimize energy consumption, which is a critical concern in industrial settings. This efficiency not only helps reduce operational costs but also contributes to sustainable practices within the foundry industry. Improved insulation materials and advanced control systems ensure that heat loss is minimized, allowing for a more efficient heating cycle.
Furthermore, the newest ladle preheaters often incorporate smart technology, enabling operators to monitor and control the heating process remotely. This functionality allows for real-time adjustments based on specific production requirements, enhancing flexibility and responsiveness in operations. By integrating digital solutions, foundries can optimize their workflows, leading to increased productivity and reduced downtime.
The benefits of implementing modern ladle preheating solutions extend beyond operational efficiency. Consistent preheating of ladles contributes to better metallurgical properties of the cast products. By maintaining the temperature of the molten metal, the risk of inclusions and other defects is significantly reduced, resulting in higher-quality outputs and improved material performance.
In conclusion, the newest ladle preheaters represent a significant advancement in the foundry and thermal treatment industries. By enhancing the preheating process, these systems not only improve the quality of cast products but also promote energy efficiency and sustainable manufacturing practices. As foundries continue to adopt these innovative technologies, they will likely see substantial improvements in both operational efficiency and product quality, making them a vital component in the future of metal casting operations.
If you are interested in our products, please leave your email and we will contact you as soon as possible.
COOKIES
Our website uses cookies and similar technologies to personalize the advertising shown to you and to help you get the best experience on our website. For more information, see our Privacy & Cookie Policy
COOKIES
Our website uses cookies and similar technologies to personalize the advertising shown to you and to help you get the best experience on our website. For more information, see our Privacy & Cookie Policy
These cookies are necessary for basic functions such as payment. Standard cookies cannot be turned off and do not store any of your information.
These cookies collect information, such as how many people are using our site or which pages are popular, to help us improve the customer experience. Turning these cookies off will mean we can't collect information to improve your experience.
These cookies enable the website to provide enhanced functionality and personalization. They may be set by us or by third-party providers whose services we have added to our pages. If you do not allow these cookies, some or all of these services may not function properly.
These cookies help us understand what you are interested in so that we can show you relevant advertising on other websites. Turning these cookies off will mean we are unable to show you any personalized advertising.