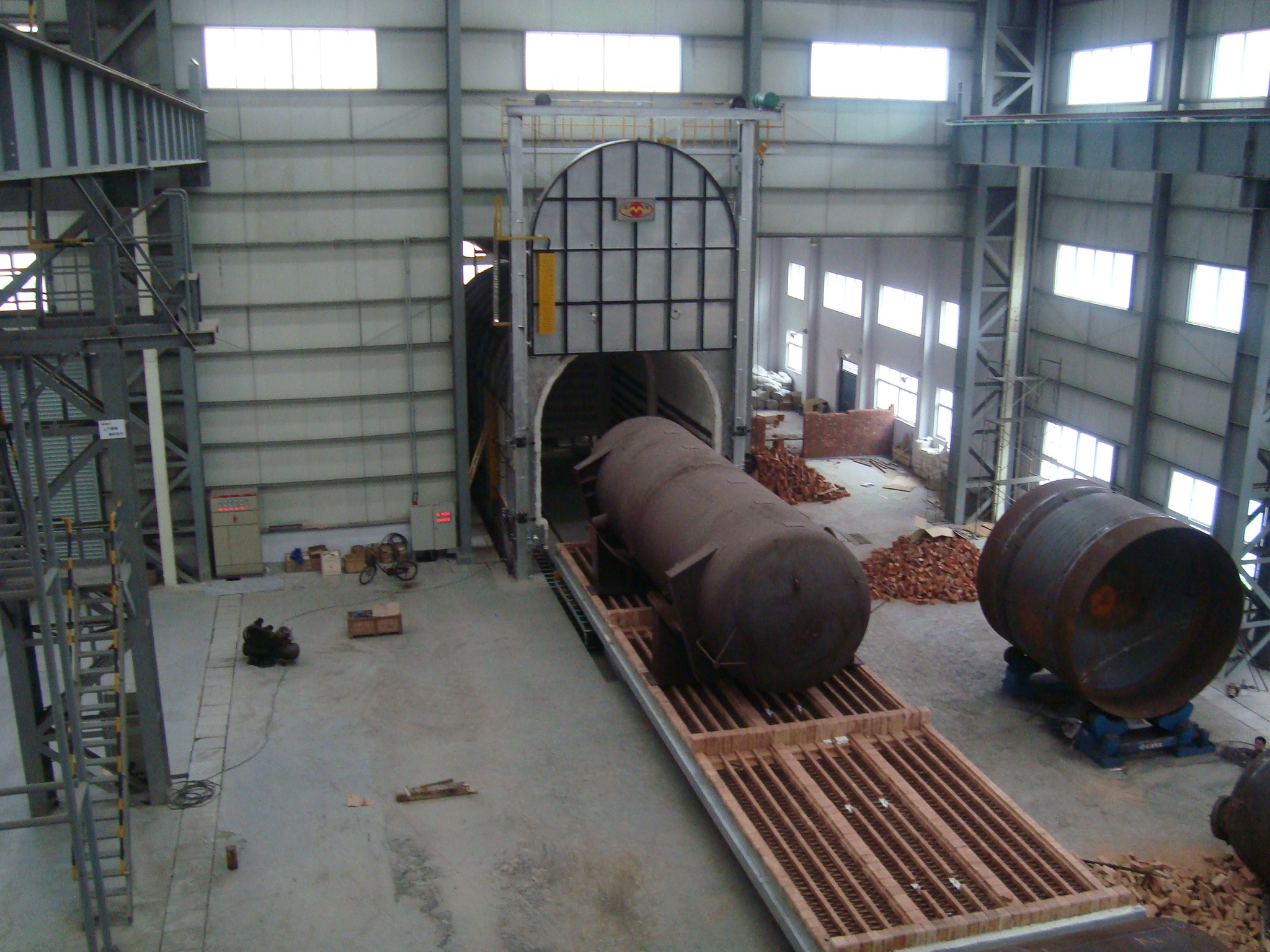


Unlocking the Secrets of Quality High Temperature Furnaces for Your Industrial Needs
Unlocking the Secrets of Quality High Temperature Furnaces for Your Industrial Needs
In the industrial sector, selecting the appropriate high-temperature furnace is pivotal to achieving desired production outcomes and maintaining operational efficiency. Furnaces play a crucial role in various processes such as casting, heat treatment, and sintering. Understanding the nuances of these robust machin
Unlocking the Secrets of Quality High Temperature Furnaces for Your Industrial Needs
In the industrial sector, selecting the appropriate high-temperature furnace is pivotal to achieving desired production outcomes and maintaining operational efficiency. Furnaces play a crucial role in various processes such as casting, heat treatment, and sintering. Understanding the nuances of these robust machines can help businesses make informed decisions that optimize performance and reduce costs. In this article, we'll delve into the key aspects of high-temperature furnaces, including types, features, applications, and best practices for maintenance and selection.
Table of Contents
1. Introduction to High Temperature Furnaces
2. Understanding the Different Types of High Temperature Furnaces
2.1 Electric Furnaces
2.2 Gas Furnaces
2.3 Induction Furnaces
3. Key Features of Quality High Temperature Furnaces
3.1 Temperature Control and Uniformity
3.2 Energy Efficiency
3.3 Safety Features
4. Applications of High Temperature Furnaces in Various Industries
4.1 Metal Casting and Heat Treatment
4.2 Ceramics and Glass Processing
4.3 Aerospace and Automotive Industries
5. Selecting the Right High Temperature Furnace for Your Needs
5.1 Assessing Your Industrial Requirements
5.2 Evaluating Suppliers and Brands
6. Best Practices for Maintenance and Performance Optimization
7. Frequently Asked Questions (FAQs)
8. Conclusion
1. Introduction to High Temperature Furnaces
High-temperature furnaces are specialized industrial equipment designed to achieve elevated temperatures for various material processing applications. These furnaces are integral to processes involving the melting, casting, and heat treatment of metals and other materials. With capabilities often exceeding 1,000 degrees Celsius, high-temperature furnaces enable manufacturers to refine materials and ensure high-quality outcomes.
In recent years, the demand for high-temperature furnaces has surged, driven by advancements in technology and the need for efficiency in industrial processes. Understanding how to select and maintain these furnaces is crucial for any business looking to enhance its operational capabilities.
2. Understanding the Different Types of High Temperature Furnaces
There are several types of high-temperature furnaces available, each designed to suit specific industrial applications. Selecting the right type can significantly impact production efficiency and product quality.
2.1 Electric Furnaces
Electric furnaces utilize electrical energy to generate heat, making them an excellent choice for applications requiring precise temperature control. These furnaces are known for their efficiency and the ability to maintain uniform heating. They are often used in smaller batch processes, such as laboratories and specialty manufacturing.
2.2 Gas Furnaces
Gas furnaces operate using natural gas or propane, which can generate high temperatures quickly. They are well-suited for large-scale operations and are commonly employed in metal casting and heat treatment applications. Gas furnaces may offer lower operational costs, especially in extensive production environments.
2.3 Induction Furnaces
Induction furnaces use electromagnetic induction to heat materials, providing rapid heating and excellent temperature control. These furnaces are particularly effective for melting metals and alloys, making them a popular choice in foundries and metalworking industries. They are recognized for their efficiency and reduced energy consumption.
3. Key Features of Quality High Temperature Furnaces
When assessing high-temperature furnaces, several key features should be considered to ensure quality and performance.
3.1 Temperature Control and Uniformity
The ability to control and monitor temperature is crucial in high-temperature furnaces. Advanced temperature control systems allow for precise adjustments, ensuring uniform heating throughout the furnace. This feature is vital for processes where material properties can be sensitive to temperature variations.
3.2 Energy Efficiency
Energy efficiency is an essential consideration, given the high operational costs associated with running high-temperature furnaces. Quality furnaces often incorporate insulation materials and advanced burner technology to minimize energy consumption and operating costs.
3.3 Safety Features
Safety is paramount in any industrial setting. Quality high-temperature furnaces should be equipped with safety features such as automatic shut-off systems, over-temperature protection, and emergency stop buttons. These features help prevent accidents and ensure a safe working environment.
4. Applications of High Temperature Furnaces in Various Industries
High-temperature furnaces find applications across a broad spectrum of industries. Understanding these applications can help businesses identify how they can leverage this technology for their specific needs.
4.1 Metal Casting and Heat Treatment
In the metalworking industry, high-temperature furnaces are essential for processes like casting and heat treatment. They allow for the melting of metals, followed by controlled cooling to enhance material properties. This process is critical for producing high-strength components for various applications.
4.2 Ceramics and Glass Processing
High-temperature furnaces are used extensively in the ceramics and glass industries for firing and sintering processes. These furnaces enable the formation of complex shapes and enhance the durability and aesthetic qualities of ceramic and glass products.
4.3 Aerospace and Automotive Industries
The aerospace and automotive sectors rely on high-temperature furnaces for manufacturing components that require exceptional strength and heat resistance. These industries benefit from advanced furnace technology that ensures consistent quality and performance in critical applications.
5. Selecting the Right High Temperature Furnace for Your Needs
Choosing the right high-temperature furnace requires careful consideration of various factors to ensure that it meets your operational needs.
5.1 Assessing Your Industrial Requirements
Begin by evaluating your specific industrial requirements, including the type of materials you will process, the necessary temperature range, and production volume. Consider whether you need a furnace for batch processing or continuous operation, as this will influence your selection.
5.2 Evaluating Suppliers and Brands
Research reputable suppliers and manufacturers of high-temperature furnaces. Look for brands with a proven track record in your industry, and consider factors such as customer support, warranty offerings, and the availability of spare parts. Reading customer reviews and testimonials can provide valuable insights into the reliability of the products.
6. Best Practices for Maintenance and Performance Optimization
Regular maintenance is essential for ensuring the longevity and performance of high-temperature furnaces. Implementing best practices can help you avoid costly repairs and downtime.
1. **Routine Inspections**: Schedule regular inspections of furnace components, including heating elements, insulation, and control systems. Early detection of wear and tear can prevent significant issues down the line.
2. **Calibration**: Regularly calibrate temperature control systems to ensure accuracy. An improperly calibrated system can lead to inconsistent results and affect product quality.
3. **Cleaning**: Maintain cleanliness within the furnace to prevent contamination and ensure efficient operation. Regular cleaning of heating elements and chamber walls can enhance performance and safety.
4. **Training**: Ensure that operators are well-trained in the proper use and maintenance of the furnace. A knowledgeable workforce can significantly impact operational efficiency and safety.
7. Frequently Asked Questions (FAQs)
1. What is the maximum temperature a high-temperature furnace can reach?
Most high-temperature furnaces can achieve temperatures exceeding 1,200 degrees Celsius, depending on the design and application.
2. How does an electric furnace differ from a gas furnace?
Electric furnaces use electrical energy to generate heat, while gas furnaces utilize natural gas or propane. Electric furnaces provide better temperature control, whereas gas furnaces often have lower operational costs for large-scale production.
3. What maintenance is required for high-temperature furnaces?
Routine inspections, calibration, cleaning, and operator training are essential maintenance practices to ensure optimal performance and longevity.
4. Can high-temperature furnaces be used for multiple applications?
Yes, many high-temperature furnaces are versatile and can be used for various applications, including metal casting, heat treatment, and material processing in ceramics and glass.
5. How can I determine the right furnace size for my needs?
Assess your production requirements, including the volume of materials to be processed and the size of the components. Consulting with a supplier can help identify the appropriate furnace size based on your specific needs.
8. Conclusion
High-temperature furnaces are indispensable tools in various industrial applications, significantly impacting production efficiency and product quality. By understanding the types of furnaces available, their key features, and best practices for maintenance, businesses can unlock the potential of these machines. In selecting the right high-temperature furnace for your industrial needs, thorough research and evaluation are crucial for ensuring long-term success. With the proper furnace technology, companies can enhance their operational capabilities and remain competitive in today's fast-paced industrial landscape.