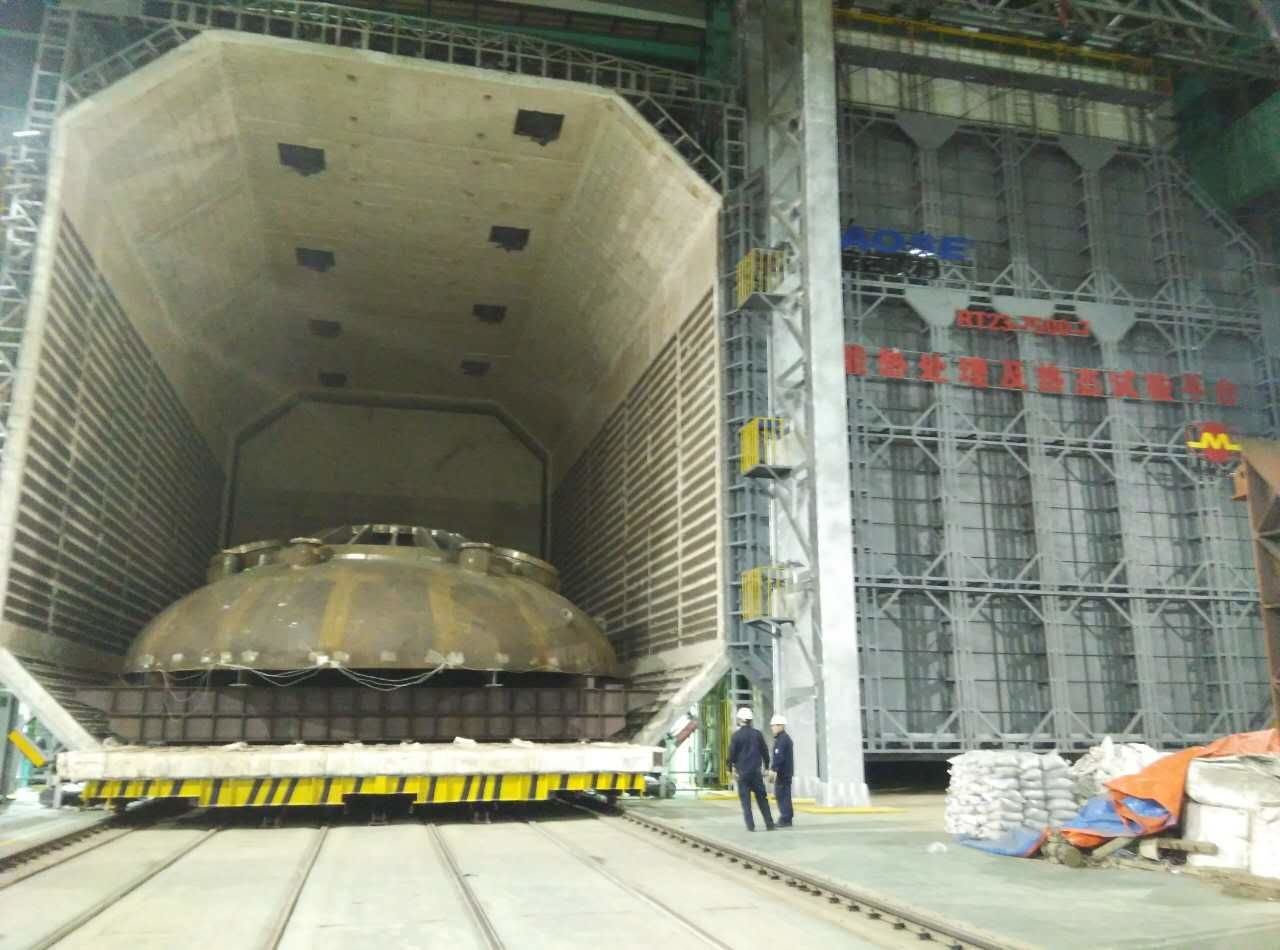


Integrating an Advanced Curing Furnace into Your Existing Production Line: A Comprehensive Guide
Integrating an Advanced Curing Furnace into Your Existing Production Line
Table of Contents
1. Introduction to Curing Furnaces
2. Benefits of an Advanced Curing Furnace
3. Key Considerations for Integration
4. Steps to Integrate an Advanced Curing Furnace
5. Maintenance and Safety Protocols
6. Optimizing Efficiency in Your Production Line
7. Common Challenges and Solut
Integrating an Advanced Curing Furnace into Your Existing Production Line
Table of Contents
- 1. Introduction to Curing Furnaces
- 2. Benefits of an Advanced Curing Furnace
- 3. Key Considerations for Integration
- 4. Steps to Integrate an Advanced Curing Furnace
- 5. Maintenance and Safety Protocols
- 6. Optimizing Efficiency in Your Production Line
- 7. Common Challenges and Solutions
- 8. Frequently Asked Questions
- 9. Conclusion
1. Introduction to Curing Furnaces
The manufacturing landscape is ever-evolving, with industries constantly seeking ways to enhance production efficiency and product quality. One significant advancement in this area is the integration of **advanced curing furnaces**. These specialized machines play a crucial role in processes like curing coatings, adhesives, and other materials that require precise thermal treatment. Understanding the fundamentals of **curing furnaces** is vital for any organization looking to stay competitive.
1.1 What is a Curing Furnace?
A curing furnace is an industrial oven designed to heat materials at controlled temperatures and durations, facilitating chemical reactions such as curing, drying, and hardening. The use of advanced technology in these furnaces allows for better temperature control, improved energy efficiency, and enhanced safety measures.
1.2 Types of Curing Furnaces
Different types of curing furnaces are available in the market, including batch, continuous, and hybrid models. Each type has its own set of advantages, and selecting the right one depends on your production needs, volume, and specific applications.
2. Benefits of an Advanced Curing Furnace
Integrating an advanced curing furnace into your production line offers numerous benefits, paving the way for increased productivity and improved product quality. Here are some of the key advantages:
2.1 Enhanced Product Quality
Advanced curing furnaces provide uniform temperature distribution, ensuring consistent curing across all materials. This uniformity results in fewer defects and higher-quality products.
2.2 Increased Production Efficiency
These furnaces are designed for high throughput and faster curing cycles, allowing manufacturers to meet rising demand without compromising quality.
2.3 Energy Efficiency
Modern curing furnaces are equipped with advanced energy-saving technologies. They use less energy compared to older models, leading to lower operational costs and a reduced carbon footprint.
2.4 Improved Workplace Safety
With state-of-the-art safety features, advanced curing furnaces minimize risks associated with high-temperature operations, thereby protecting workers and reducing liability.
3. Key Considerations for Integration
Before integrating an advanced curing furnace into your production line, several factors need to be carefully evaluated to ensure a smooth transition.
3.1 Compatibility with Existing Systems
Assess how well the new furnace will fit into your current production setup. Evaluate compatibility with other equipment and the overall workflow.
3.2 Space Requirements
Determine the space needed for the new furnace. Ensure that there is adequate room for the equipment itself, as well as for maintenance and safety clearance.
3.3 Budget Constraints
Consider the total cost of ownership, including installation, maintenance, and energy consumption. A detailed cost analysis will help in making an informed decision.
3.4 Employee Training
Training staff on how to operate and maintain the new furnace is crucial. This will not only ensure safety but also maximize the efficiency of your production line.
4. Steps to Integrate an Advanced Curing Furnace
Successfully integrating an advanced curing furnace requires careful planning and execution. Here are the essential steps to follow:
4.1 Identify Your Needs
Analyze your production requirements to determine the specifications needed for the curing furnace. This includes temperature ranges, capacity, and desired features.
4.2 Select the Right Furnace
After identifying your needs, research and select a furnace that meets your specifications. Consult with manufacturers and consider customer reviews for insights.
4.3 Plan the Installation
Create a detailed installation plan that includes timelines, personnel, and resources needed for a successful setup.
4.4 Conduct Testing and Calibration
Once the furnace is installed, conduct thorough testing and calibration to ensure it operates correctly and meets all production requirements.
4.5 Train Your Team
Organize training sessions for your workforce to familiarize them with the new equipment. This should include operational procedures, maintenance routines, and safety protocols.
4.6 Monitor Performance
After integration, closely monitor the furnace's performance. Gather data on production efficiency, product quality, and energy usage to identify areas for further optimization.
5. Maintenance and Safety Protocols
Maintaining an advanced curing furnace is essential for its longevity and efficiency. Implementing rigorous safety protocols is equally critical to safeguard your employees and production line.
5.1 Regular Maintenance Checks
Schedule routine maintenance checks to ensure all components function correctly. This should include inspections of heating elements, thermostats, and control systems.
5.2 Safety Protocols
Establish clear safety protocols regarding the operation of the furnace. This includes emergency procedures, personal protective equipment (PPE) requirements, and guidelines for handling materials.
5.3 Documentation
Keep detailed records of all maintenance activities and safety checks. This documentation can be invaluable for regulatory compliance and continuous improvement efforts.
6. Optimizing Efficiency in Your Production Line
Once the advanced curing furnace is integrated, various strategies can be employed to optimize its efficiency.
6.1 Continuous Process Improvement
Utilize lean manufacturing principles to continuously assess and improve the workflow around the curing furnace. Identify bottlenecks and implement strategies to streamline operations.
6.2 Data Analytics
Leverage data analytics to monitor production metrics. Analyzing data helps in making informed decisions and identifying trends that can enhance efficiency.
6.3 Employee Feedback
Encourage feedback from employees who operate the curing furnace. Their insights can provide valuable information for improving processes and safety measures.
7. Common Challenges and Solutions
Integrating an advanced curing furnace is not without its challenges. Here are some common issues faced and potential solutions.
7.1 Resistance to Change
Employees may resist new technology due to fear of the unknown. Mitigate this by providing comprehensive training and emphasizing the benefits of the new system.
7.2 Technical Issues
Technical problems may arise during integration. Work closely with the furnace manufacturer for troubleshooting and prompt support.
7.3 Adjustment Period
There may be an adjustment period where production efficiency dips. Set realistic expectations and monitor performance closely during this phase.
8. Frequently Asked Questions
8.1 What is the lifespan of an advanced curing furnace?
The lifespan can vary based on usage and maintenance but generally ranges between 10 to 15 years with proper care.
8.2 How do I know if my existing production line is compatible with a new curing furnace?
Conduct a thorough analysis of your current equipment and workflows. Consult with experts to assess compatibility.
8.3 Can I retrofit my existing furnace with advanced technology?
In some cases, retrofitting is possible. Consult with your furnace manufacturer to explore available upgrades.
8.4 What are the energy savings associated with advanced curing furnaces?
Energy savings vary by model but can be significant, often reducing energy costs by 20-30% compared to older models.
8.5 How frequently should I conduct maintenance on my curing furnace?
Regular maintenance checks should be scheduled at least quarterly, with more frequent inspections during heavy usage periods.
9. Conclusion
Incorporating an advanced curing furnace into your production line is a strategic move that can enhance efficiency, improve product quality, and provide a safer work environment. By understanding the benefits, carefully considering integration factors, and following a structured implementation plan, manufacturers can achieve significant operational improvements. Remember that continuous monitoring, employee training, and maintenance are key to ensuring your new furnace performs optimally and delivers the expected return on investment. With the right approach, you can set your production line on a path toward sustained success and innovation.