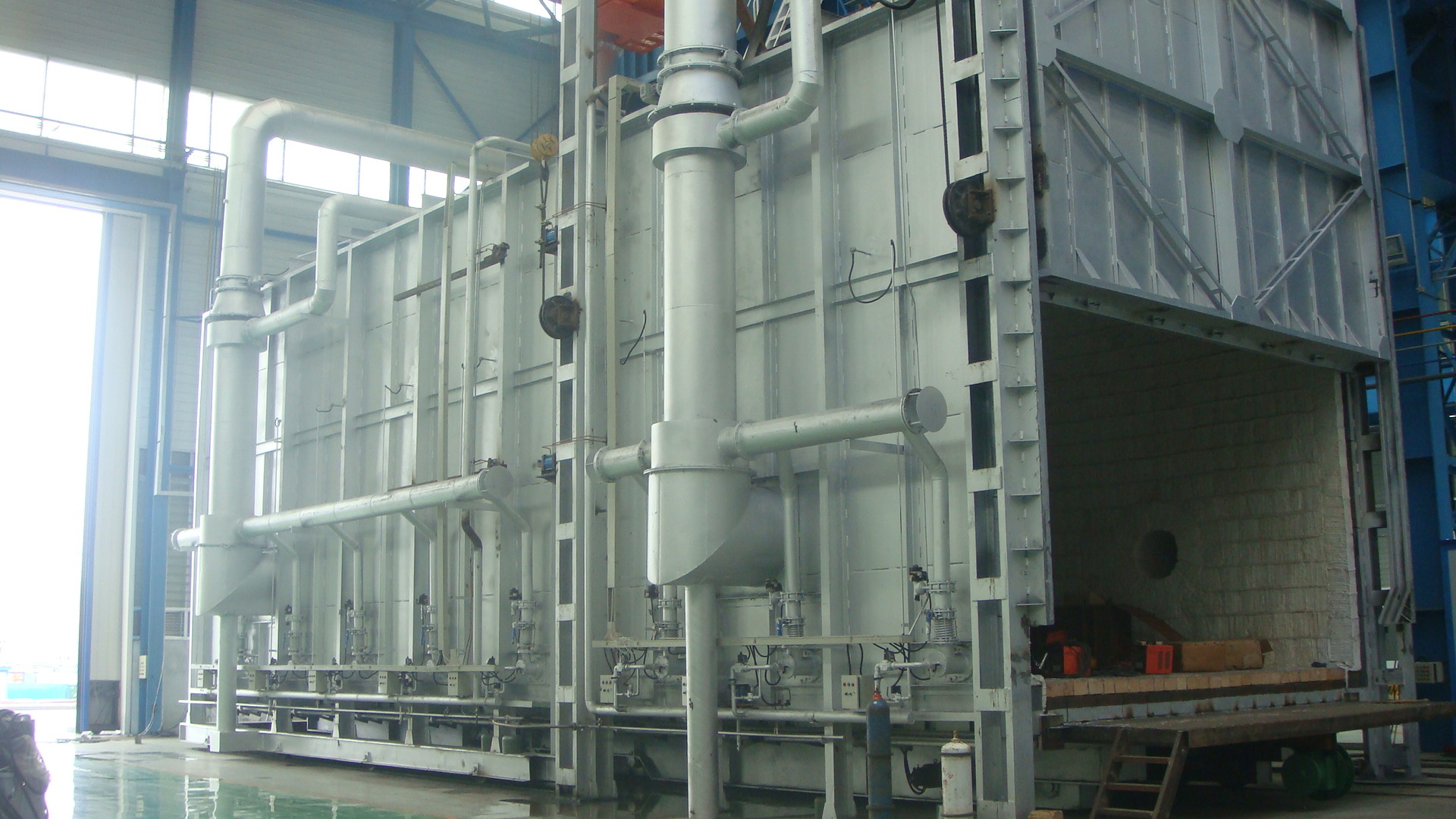


Unlocking Efficiency: The Benefits of Customized Heat Treatment Equipment
Unlocking Efficiency: The Benefits of Customized Heat Treatment Equipment
In the ever-evolving landscape of industrial manufacturing, efficiency and precision are paramount. One pivotal factor that can significantly enhance these aspects is the use of customized heat treatment equipment. This article delves into the myriad benefits of bespoke heat treatment solutions, exploring their applications and how they can transform your operational efficiency. Let’s examine the compelling reasons why investing in customized equipment is a strategic move for businesses looking to optimize their production processes.
The Importance of Heat Treatment in Manufacturing
Heat treatment plays a crucial role in altering the physical and sometimes chemical properties of materials, primarily metals. By heating and cooling materials under controlled conditions, manufacturers can achieve desired characteristics such as improved strength, hardness, ductility, and resistance to wear and corrosion. Understanding the significance of heat treatment is essential to appreciate the advantages of customized equipment.
What is Customized Heat Treatment Equipment?
Customized heat treatment equipment refers to machines and systems specifically designed and tailored to meet the unique requirements of a manufacturing process. These tailored solutions consider factors such as the type of materials being treated, the desired properties, and the scale of production. Unlike standard equipment, customized solutions are engineered to optimize efficiency, reduce waste, and enhance product quality.
Key Benefits of Customized Heat Treatment Equipment
1. Enhanced Efficiency
One of the most significant advantages of customized heat treatment equipment is the enhancement of operational efficiency. By designing equipment that aligns with specific production needs, companies can streamline processes and reduce cycle times. This efficiency translates to higher output rates, allowing businesses to meet growing consumer demands without sacrificing quality.
2. Tailored Solutions for Unique Materials
Each material has distinct properties that require specific heat treatment processes. Customized equipment caters to these unique requirements, ensuring that the treatment process is optimized for the particular characteristics of the material. This tailored approach not only improves the effectiveness of the treatment but also minimizes the risk of defects and failures.
3. Quality Consistency
Consistency in product quality is vital in manufacturing. Customized heat treatment equipment is designed to provide uniform heating and cooling, which leads to consistent results across batches. This reliability is essential for maintaining product integrity and meeting stringent industry standards.
4. Cost-Effectiveness
While the initial investment in customized equipment may be higher than standard options, the long-term savings can be substantial. Enhanced efficiency, reduced scrap rates, and improved product quality all contribute to cost savings over time. Additionally, customized solutions can lead to lower operational costs due to reduced energy consumption and maintenance needs.
5. Flexibility and Adaptability
In today’s rapidly changing market, flexibility is key. Customized heat treatment equipment can be designed with adaptability in mind, allowing manufacturers to adjust their processes as needed. This flexibility enables businesses to respond quickly to market demands or changes in material specifications without the need for significant equipment overhauls.
Applications of Customized Heat Treatment Equipment
The versatility of customized heat treatment equipment allows it to be utilized across various industries. Here are some key applications:
1. Aerospace Industry
In the aerospace sector, material performance is critical. Customized heat treatment equipment is used to treat high-strength alloys and components to ensure safety and reliability in flight. The precise control of temperature and atmosphere in these processes is essential for achieving the desired mechanical properties.
2. Automotive Manufacturing
The automotive industry demands high-quality components that can withstand harsh conditions. Customized heat treatment solutions are employed to enhance the durability and performance of gear parts, crankshafts, and other critical components, ensuring they meet rigorous safety standards.
3. Tool and Die Manufacturing
Tools and dies require precise heat treatment to achieve optimal hardness and toughness. Customized equipment allows manufacturers to tailor the heat treatment process, ensuring that tools perform reliably and have an extended service life.
4. Oil and Gas Industry
In the oil and gas sector, components are subjected to extreme conditions. Customized heat treatment equipment is essential for treating materials used in drilling and extraction operations, enhancing resistance to corrosion and wear.
Choosing the Right Customized Heat Treatment Equipment
Investing in customized heat treatment equipment requires careful consideration. Here are several factors to evaluate when selecting the right solution for your needs:
1. Process Requirements
Understand the specific heat treatment processes required for your materials. This includes temperature ranges, heating and cooling rates, and the atmosphere in which treatments will occur. Customizing equipment to fit these parameters is critical for achieving optimal results.
2. Material Specifications
Different materials respond differently to heat treatment. Ensure the equipment can accommodate the range of materials your production involves. This adaptability will contribute to efficiency and quality improvements.
3. Production Volume
Consider the scale of production. Customized equipment can be designed for high-volume operations or smaller, specialized runs. Aligning the equipment with your production goals is essential for maximizing investment returns.
4. Regulatory Compliance
Ensure that the customized heat treatment equipment meets industry regulations and standards. Compliance is crucial for maintaining product certifications and ensuring market acceptance.
Future Trends in Customized Heat Treatment Equipment
The landscape of heat treatment equipment is continuously evolving. Several trends are shaping the future of customized solutions:
1. Automation and Industry 4.0
The integration of automation and smart technology into heat treatment processes is on the rise. Customized equipment that incorporates sensors and data analytics can provide real-time monitoring and adjustments, enhancing efficiency and reducing human error.
2. Eco-Friendly Solutions
With growing environmental concerns, there is a push for eco-friendly heat treatment solutions. Customized equipment can be designed to minimize energy consumption and emissions, aligning with sustainable manufacturing practices.
3. Advanced Materials
The development of advanced materials, such as composites and high-performance alloys, requires innovative heat treatment approaches. Customized equipment will play a crucial role in processing these materials effectively.
Case Studies: Success Stories with Customized Heat Treatment Equipment
To illustrate the effectiveness of customized heat treatment equipment, let’s explore some success stories:
1. Aerospace Component Manufacturer
A leading aerospace manufacturer implemented a customized heat treatment system tailored for titanium components. The new equipment reduced cycle times by 30% and improved the mechanical properties of the materials, resulting in higher-quality components that passed stringent testing.
2. Automotive Parts Supplier
An automotive parts supplier invested in customized equipment for heat treating gears. The tailored solution enhanced durability and reduced scrap rates, leading to significant cost savings and increased customer satisfaction.
FAQs about Customized Heat Treatment Equipment
1. What types of materials can be treated with customized heat treatment equipment?
Customized heat treatment equipment can be designed to treat a wide range of materials, including various steels, aluminum alloys, titanium, and other metal composites, depending on specific process needs.
2. How does customized equipment improve efficiency?
By aligning the equipment with specific production requirements, the processes are streamlined, reducing cycle times and waste while enhancing quality and output rates.
3. Is customized heat treatment equipment more expensive than standard options?
While the initial investment may be higher, the long-term benefits such as reduced operational costs, improved efficiency, and enhanced product quality often outweigh the initial expense.
4. Can customized heat treatment equipment be adapted for future needs?
Many customized solutions are designed with flexibility in mind, allowing for adjustments and upgrades as production needs evolve or new materials are introduced.
5. What industries benefit most from customized heat treatment equipment?
Industries such as aerospace, automotive, tool and die manufacturing, and oil and gas significantly benefit from customized heat treatment solutions due to their stringent quality and performance requirements.
Conclusion
Customized heat treatment equipment represents a transformative opportunity for manufacturers aiming to enhance efficiency, consistency, and product quality. By investing in tailored solutions, businesses can reap significant benefits, from reduced operational costs to improved material performance. As industries continue to evolve, the demand for customized solutions will only grow, making it essential for manufacturers to stay ahead of the curve. Embracing customized heat treatment solutions not only ensures compliance with industry standards but also positions manufacturers for success in an increasingly competitive landscape.