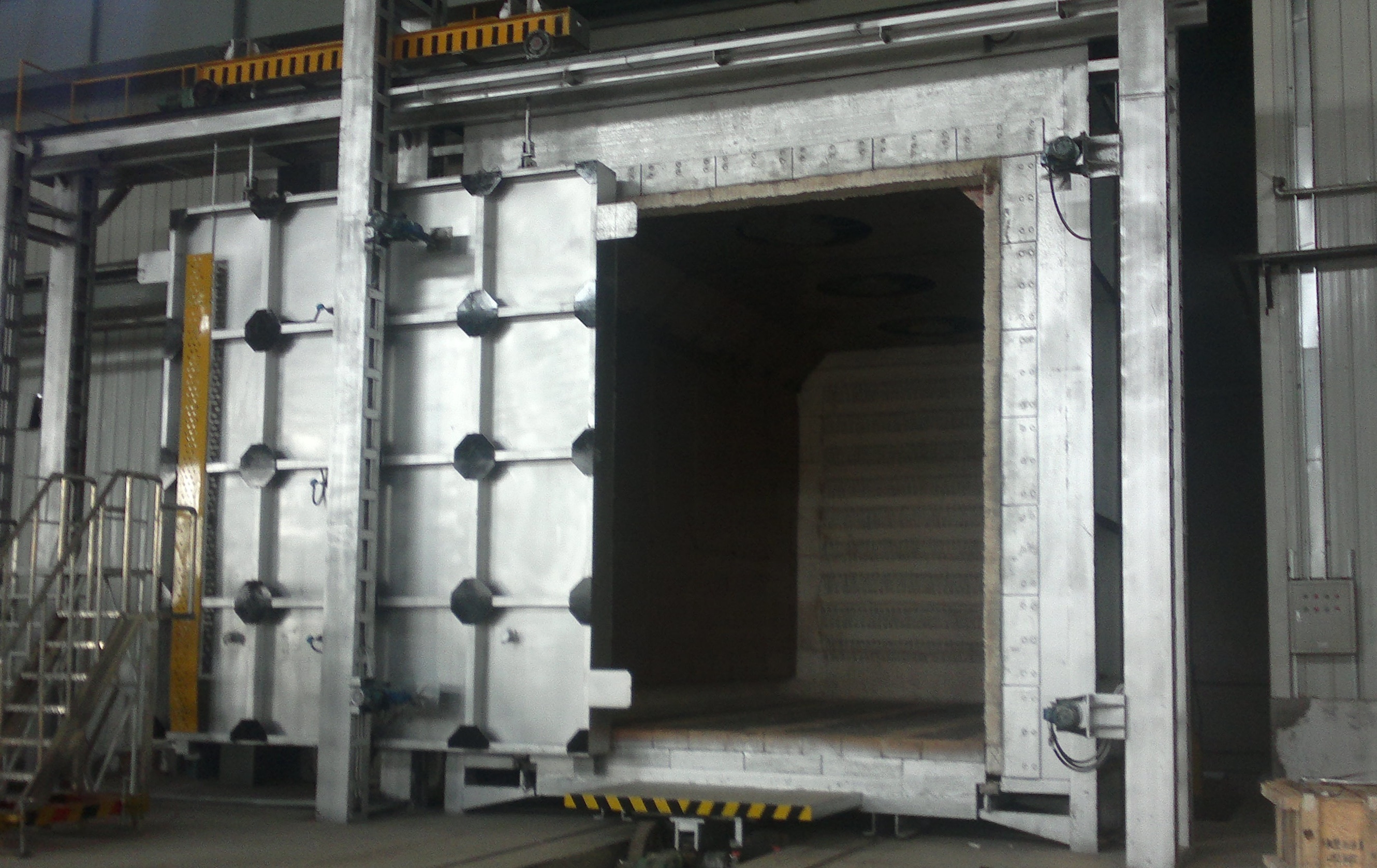


Unlocking Efficiency: The Essential Impact of Quality Vacuum Quenching Furnaces in Modern Manufacturing
Unlocking Efficiency: The Essential Impact of Quality Vacuum Quenching Furnaces in Modern Manufacturing
Table of Contents
1. Introduction to Vacuum Quenching Furnaces
2. Understanding Vacuum Quenching Processes
2.1 Principles of Vacuum Quenching
2.2 Importance of Vacuum Quenching in Manufacturing
3. Benefits of Quality Vacuum Quenching Furnace
Unlocking Efficiency: The Essential Impact of Quality Vacuum Quenching Furnaces in Modern Manufacturing
Table of Contents
- 1. Introduction to Vacuum Quenching Furnaces
- 2. Understanding Vacuum Quenching Processes
- 3. Benefits of Quality Vacuum Quenching Furnaces
- 3.1 Enhanced Product Quality
- 3.2 Energy Efficiency and Cost Reduction
- 3.3 Reduced Environmental Impact
- 4. Applications of Vacuum Quenching Furnaces
- 5. Choosing the Right Vacuum Quenching Furnace
- 6. Future Trends in Vacuum Quenching Technologies
- 7. Frequently Asked Questions (FAQs)
- 8. Conclusion
1. Introduction to Vacuum Quenching Furnaces
In the world of modern manufacturing, efficiency and quality have become paramount. One of the key technologies driving these improvements is the vacuum quenching furnace. These sophisticated machines provide a controlled environment that significantly enhances the heat treatment processes of various materials. By understanding the essential role of vacuum quenching furnaces, manufacturers can unlock new levels of efficiency and product excellence.
2. Understanding Vacuum Quenching Processes
2.1 Principles of Vacuum Quenching
Vacuum quenching involves heating components to high temperatures in a vacuum environment, followed by rapid cooling. This process is crucial for achieving the desired mechanical properties in metals and alloys. Unlike conventional quenching methods that often rely on liquid mediums like oil or water, vacuum quenching eliminates contamination and oxidation, resulting in superior material integrity.
2.2 Importance of Vacuum Quenching in Manufacturing
The significance of vacuum quenching in manufacturing cannot be overstated. It not only allows for precise control over the heating and cooling rates but also enhances the material properties, such as hardness and toughness. This is particularly vital in industries where performance and safety are critical, such as aerospace and medical applications.
3. Benefits of Quality Vacuum Quenching Furnaces
3.1 Enhanced Product Quality
One of the primary benefits of using quality vacuum quenching furnaces is the enhancement of product quality. With no oxidation or contamination risks, manufacturers can achieve cleaner, better-performing components. This leads to fewer defects and ultimately increases customer satisfaction.
3.2 Energy Efficiency and Cost Reduction
Quality vacuum quenching furnaces are designed to be energy efficient. They often utilize advanced insulation materials and recycling systems that minimize energy consumption. By reducing operational costs, manufacturers can improve their bottom line and invest in further technological advancements.
3.3 Reduced Environmental Impact
In today’s eco-conscious world, the environmental impact of manufacturing processes is under scrutiny. Vacuum quenching furnaces produce less waste and use fewer harmful chemicals compared to traditional quenching methods. This aligns with global efforts to promote sustainable manufacturing practices.
4. Applications of Vacuum Quenching Furnaces
4.1 Aerospace Industry
The aerospace industry demands the highest standards of quality and performance. Vacuum quenching furnaces are essential in the production of critical components such as turbine blades and landing gear, where precision and reliability are non-negotiable.
4.2 Automotive Industry
In automotive manufacturing, vacuum quenching is utilized for producing high-performance components like gears and shafts. The ability to achieve superior hardness and wear resistance directly contributes to vehicle safety and longevity.
4.3 Medical Equipment Manufacturing
The medical sector increasingly relies on vacuum quenching for manufacturing surgical instruments and implants. The process ensures that these products meet stringent safety standards while maintaining necessary mechanical properties.
5. Choosing the Right Vacuum Quenching Furnace
5.1 Key Features to Consider
When selecting a vacuum quenching furnace, several key features should be considered. These include the furnace's temperature range, cooling rates, and the specific materials it can handle. Additionally, automation features and user-friendly controls can greatly enhance operational efficiency.
5.2 Evaluating Cost-Effectiveness
Investing in a vacuum quenching furnace can require a significant upfront cost. However, evaluating the long-term benefits, such as reduced energy consumption and improved product quality, is crucial for assessing overall cost-effectiveness. Manufacturers should conduct a thorough analysis to ensure that their investment will yield substantial returns.
6. Future Trends in Vacuum Quenching Technologies
As technology evolves, so too do vacuum quenching processes. Future trends indicate a shift toward more automation and integration with Industry 4.0 technologies. Smart furnaces equipped with data analytics and IoT capabilities will enhance real-time monitoring and control, further optimizing efficiency and product quality.
7. Frequently Asked Questions (FAQs)
What is a vacuum quenching furnace?
A vacuum quenching furnace is a specialized heat treatment equipment that heats materials in a vacuum environment and then cools them rapidly, enhancing material properties.
How does vacuum quenching differ from traditional quenching methods?
Unlike traditional methods that use liquids for cooling, vacuum quenching eliminates the risk of oxidation and contamination by operating in a vacuum, resulting in higher quality components.
What are the primary benefits of vacuum quenching?
The primary benefits include improved product quality, energy efficiency, reduced environmental impact, and enhanced mechanical properties of treated materials.
In which industries are vacuum quenching furnaces commonly used?
Vacuum quenching furnaces are commonly used in aerospace, automotive, and medical equipment manufacturing, among other high-precision industries.
What should I consider when purchasing a vacuum quenching furnace?
Consider factors such as temperature range, cooling capabilities, energy efficiency, and available automation features to ensure the selected furnace meets your manufacturing needs.
8. Conclusion
In conclusion, quality vacuum quenching furnaces play a pivotal role in modern manufacturing, unlocking unparalleled efficiency and product quality. By understanding the principles, benefits, and applications of these advanced technologies, manufacturers can make informed decisions that lead to enhanced performance and competitiveness in the market. As we embrace future advancements in vacuum quenching, the potential for improved manufacturing processes continues to grow, paving the way for even greater achievements in various industries. Investing in quality vacuum quenching technology is not just a choice but a strategic move toward ensuring excellence and sustainability in manufacturing.